Introduction:-
Welcome to our comprehensive guide on selecting the right sampling valve for your industrial process. Whether you are an engineer or an individual involved in industrial processes, understanding valve types and their applications is crucial for ensuring efficient and reliable operations. In this blog, we will explore the factors you need to consider when selecting a sampling valve, delve into different valve construction materials and their applications, analyze operational requirements, and provide a step-by-step guide to valve selection. By the end of this guide, you will have a thorough understanding of sampling valves and be equipped with the knowledge to make informed decisions for your specific process needs. Let’s dive in!
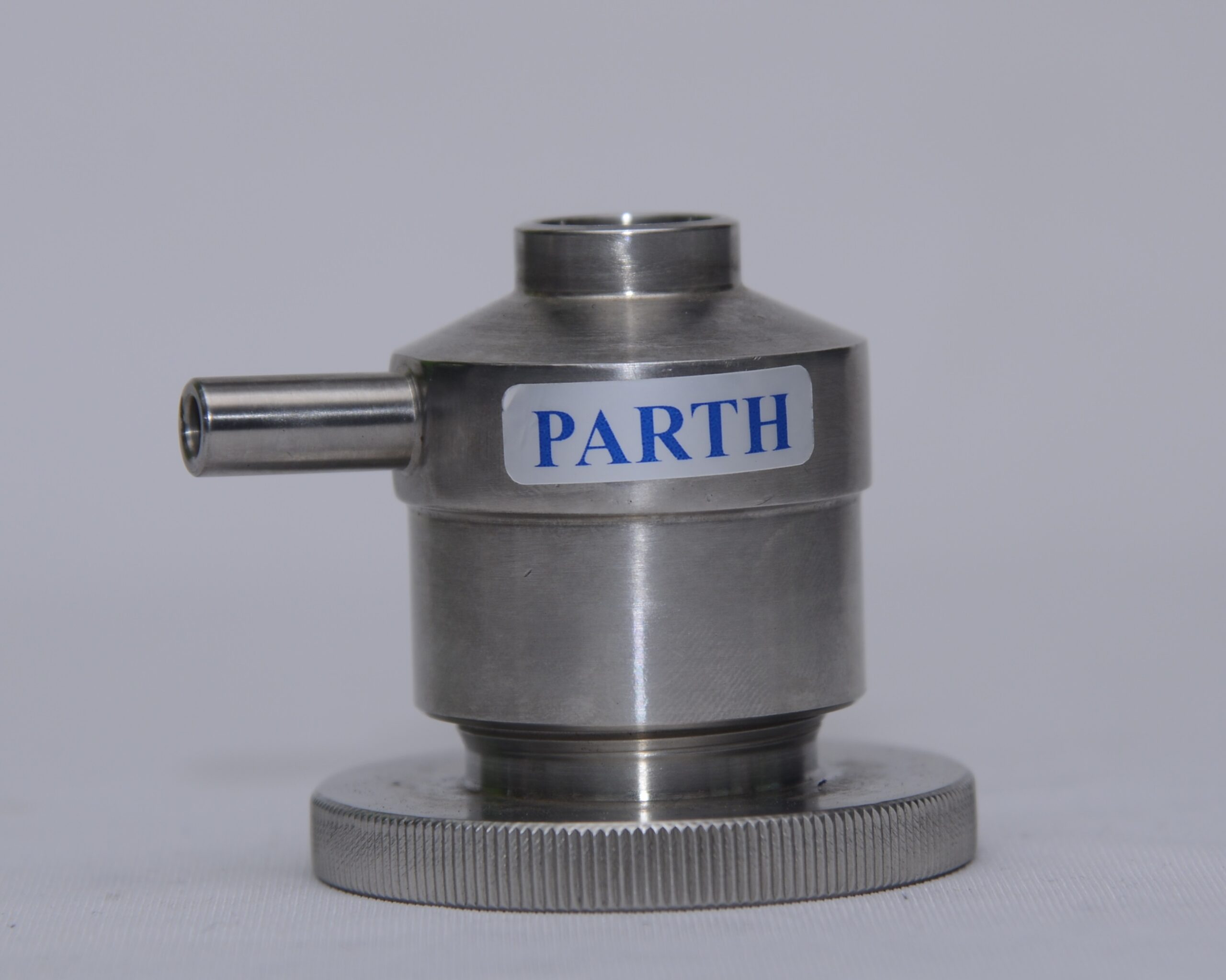
Sampling Valve
1. Understanding Valve Types: A Comprehensive Overview
Valves play a crucial role in industrial processes by controlling the flow of various mediums in a piping system. They are used to stop and start the flow of media and can also control the rate of flow. Choosing the appropriate valve for a specific application is essential for ensuring efficiency and safety.
There are different types of valves available, and understanding their characteristics is crucial for selecting the right valve for a specific application. Valves can be classified into three categories: rotary, linear, and self-actuated.
Rotary valves, also known as quarter-turn valves, utilize a rotating closure component to block flow within a piping system. These valves are closed at 0 degrees and open at 90 degrees. They are commonly used in applications where quick and efficient flow control is required.
Linear valves, on the other hand, use a linear motion to control the flow. These valves are operated by a stem or a plunger that moves in a straight line to open or close the valve. Linear valves are often used in applications where precise control of the flow rate is necessary.
2. Factors to Consider When Selecting a Sampling Valve
When it comes to selecting a sampling valve for industrial applications, several factors need to be considered. This is particularly important in light of the issues plaguing the industrial valve industry, such as the sale of remanufactured and poor-quality valves that can compromise engineering safety.
Understanding the specific usage and environment of the valve is crucial in choosing the right type, size, and design to meet operational requirements. Valves can have various purposes, including regulating pressure, controlling flow, and isolating equipment. By identifying the precise usage and purpose of the valve, individuals involved in industrial processes can make informed decisions about the type of valve that will best serve their needs.
By considering factors such as operational conditions, construction material, and operational requirements, individuals can make informed decisions about the best sampling valve for their specific needs.
In the next section, we will explore the different types of sampling valves available and their specific features and advantages.
3. Exploring Different Valve Construction Materials and Their Applications
In the previous section, we explored the different types of valves and their components. Now, let’s delve into the world of valve construction materials and their applications in industrial systems.
Choosing the right construction material for valves is crucial for ensuring the efficiency and reliability of industrial processes. The operational conditions, such as temperature, pressure, and the type of fluid or gas being controlled, play a significant role in determining the appropriate material for valve construction.
Valve bodies, being the main housing of the valve, require careful material selection. They need to withstand the operational requirements and provide a strong and durable structure. Common materials used for valve bodies include stainless steel, cast iron, brass, and bronze. Each material has its advantages and is chosen based on factors such as corrosion resistance, strength, and cost-effectiveness.
By carefully considering the construction materials for each component of a valve, industrial fluid, and analytical sampling system, professionals can ensure optimal performance and longevity. The appropriate material selection minimizes the risk of contamination, enhances cleanability, and ensures the valve can withstand the specific operational requirements.
In the next section, we will explore the different valve types and their applications in more detail, highlighting the importance of selecting the right valve for specific industrial processes.
4. Analyzing Operational Requirements: Matching Valve Types to Process Conditions
Understanding the importance of selecting the right valve type for specific process conditions is crucial for individuals involved in industrial processes, especially engineers. The impact of using the wrong valve type can have significant consequences on operational efficiency and safety.
When analyzing operational requirements, it is essential to explore different valve types and their suitability for various process conditions. Factors such as pressure, temperature, and flow rate play a significant role in determining the appropriate valve type. Real-world examples of the consequences of mismatching valve types to process conditions highlight the importance of selecting the right valve type.
Properly matching valve types to process conditions brings several benefits, including improved performance and reduced maintenance costs. Selecting and installing valves based on process conditions requires following best practices and considering factors such as construction material, operational requirements, and available options.
5. A Step-by-Step Guide to Valve Selection: From Sizing to Installation
Proper valve selection is crucial in industrial processes to ensure smooth and efficient operations. In the previous section, we discussed the step-by-step process of valve selection, starting from sizing to installation. Now, let’s delve deeper into each of these steps to understand their significance and how they contribute to the overall success of your process.
The first step in valve selection is determining the correct valve size for your application. This involves considering factors such as flow rate, pressure drop, and system requirements. Sizing the valve accurately is essential to ensure optimal performance and prevent any potential issues in the future.
Next, it’s important to understand the different types of valves available and their specific applications. Valves come in various designs, including ball valves, check valves, diaphragm valves, elliptic valves, metering valves, needle valves, pinch valves, plug valves, pressure valves, and sampling valves. Each type has its unique features and functions, and selecting the right valve type is crucial for achieving the desired performance.
In the next section, we will explore in more detail the different types of valves and their specific applications, providing you with a comprehensive understanding of valve selection for industrial processes.
Conclusion:-
In conclusion, selecting the right sampling valve for your industrial process is a critical decision that can greatly impact the efficiency and reliability of your operations. By understanding valve types, construction materials, and operational requirements, you can make informed decisions that ensure optimal performance. This comprehensive guide has provided you with the knowledge and tools necessary to navigate the valve selection process, from considering factors to step-by-step guidance. Armed with this information, you can confidently choose the sampling valve that best suits your specific process needs. Remember, a well-chosen sampling valve is the key to achieving efficient and reliable operations in your industrial process. Good luck!
To Know More
www.parthvalve.com/sampling-valve